Track & Trace est sur toutes les lèvres depuis un certain temps déjà, mais de quoi s'agit-il en réalité ? La plupart du temps, il s'agit de l'identification des différents produits, de la traçabilité des données de production et de qualité ainsi que des canaux de vente. Les conditions préalables à la mise en œuvre de Track & Trace sont le marquage des produits, des systèmes de caméra et d'identification appropriés ainsi que la disponibilité des données.
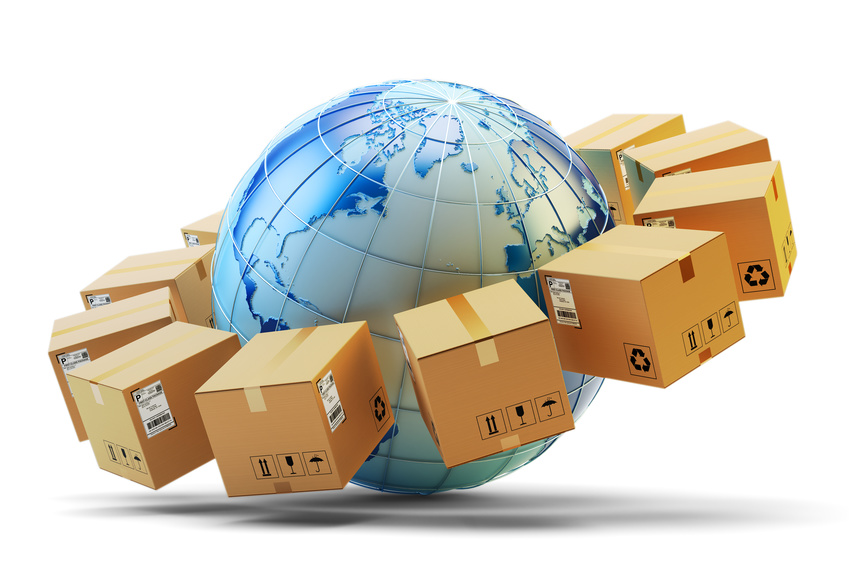
Qu'est-ce que le "Track & Trace" ?
Le terme Track & Trace vient à l'origine du domaine de la logistique. Il s'agit tout d'abord de la traçabilité des envois : quand un colis a-t-il été collecté, quand est-il arrivé à l'aéroport de destination, etc. Très rapidement, ce terme est devenu un concept qui englobe également d'autres domaines. Il désigne notamment la traçabilité des différentes étapes de la production, de l'approvisionnement en matières premières, des données de production et de qualité et des canaux de vente. Track & Trace se réfère donc à l'ensemble de la "chaîne d'approvisionnement".
Conditions préalables et objectifs
L'une des premières exigences du Track & Trace est l'identification explicite d'un produit. Pour les produits de grande série, le marquage est effectué sur le produit lui-même (Direct Part Marking) ou, si cela n'est pas possible ou trop coûteux, sur son emballage. Le marquage est apposé par le fabricant et doit pouvoir être lu ultérieurement de manière sûre partout dans le monde. Il est désormais possible de collecter et d'enregistrer des données sur chaque produit. Ces données doivent être disponibles et consultables en cas de besoin. L'industrie pharmaceutique est l'un des principaux acteurs de la traçabilité.
Il y a plusieurs raisons pour lesquelles les entreprises misent aujourd'hui sur le Track & Trace. Les aspects importants sont la sécurité contre la contrefaçon, la fiabilité du produit et le suivi du parcours d'un produit jusqu'au magasin. L'enregistrement en ligne des données de production permet bien entendu d'optimiser encore davantage le processus.
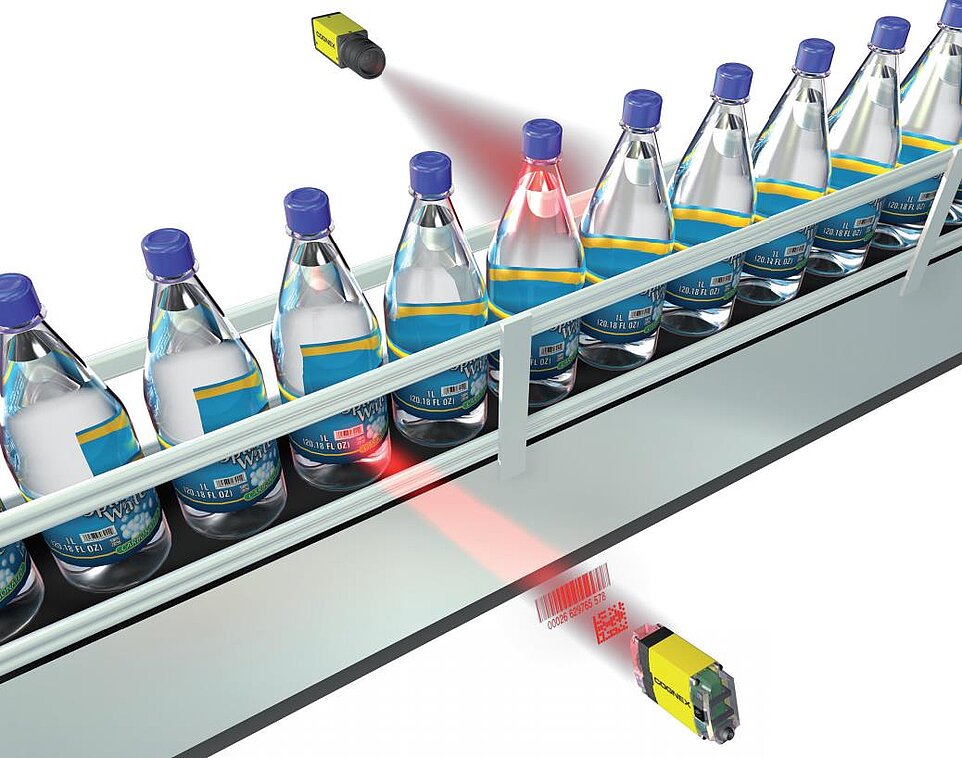

Type de marquage
L'inscription en caractères explicites est le mode d'identification traditionnel. Elle a l'avantage de pouvoir être relue par des personnes sans accessoires, mais elle est moins adaptée à une identification automatique. Il existe néanmoins des solutions proposées par des spécialistes qui conviennent à l'environnement industriel, comme le montre l'exemple des conteneurs. Il s'agit ici d'identifier le contenu d'un conteneur à l'aide de ses inscriptions sur le panneau de documentation. Cela est réalisé à l'aide d'un système de caméra et d'un logiciel de lecture (OCR pour Optical Character Recognition) qui extrait et lit les caractères de l'image.
La méthode de marquage la plus courante pour l'identification par machine est toujours le code-barres linéaire. Les lecteurs sont de plus en plus souvent équipés de capteurs d'imagerie. Par rapport aux scanners laser, les appareils de nouvelle génération offrent une meilleure sécurité de lecture en cas de codes endommagés et une plus grande flexibilité, car avec ces appareils, le code peut être placé et tourné n'importe où dans le champ de la caméra. Le contenu informatif des codes linéaires est toutefois plutôt modeste pour un encombrement relativement important.
Les codes bidimensionnels sont une évolution qui a fait ses preuves. Ceux-ci utilisent beaucoup mieux la surface disponible et leur contenu informatif est massivement plus important pour un encombrement moindre. De plus, ces codes peuvent être lus de manière beaucoup plus sûre, car ils disposent d'une grande redondance qui est utilisée dans les procédures de correction des erreurs. Même des codes endommagés peuvent encore souvent être lus en toute sécurité. Parmi les codes 2D, le code DataMatrix ECC200 s'est solidement établi et est même prescrit par la loi dans l'industrie pharmaceutique pour le marquage des emballages.
Il existe en outre d'autres procédés d'identification, comme la RFID ou des procédés propriétaires. Cependant, l'apposition d'un code sur une étiquette ou sur un produit est généralement le moyen d'identification le plus simple et le moins coûteux.
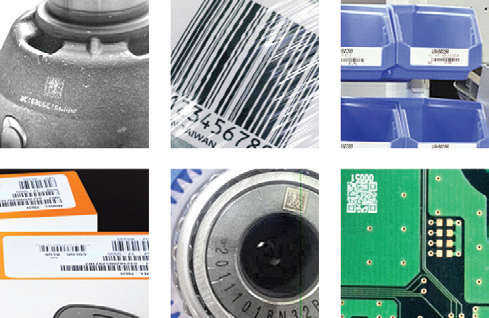
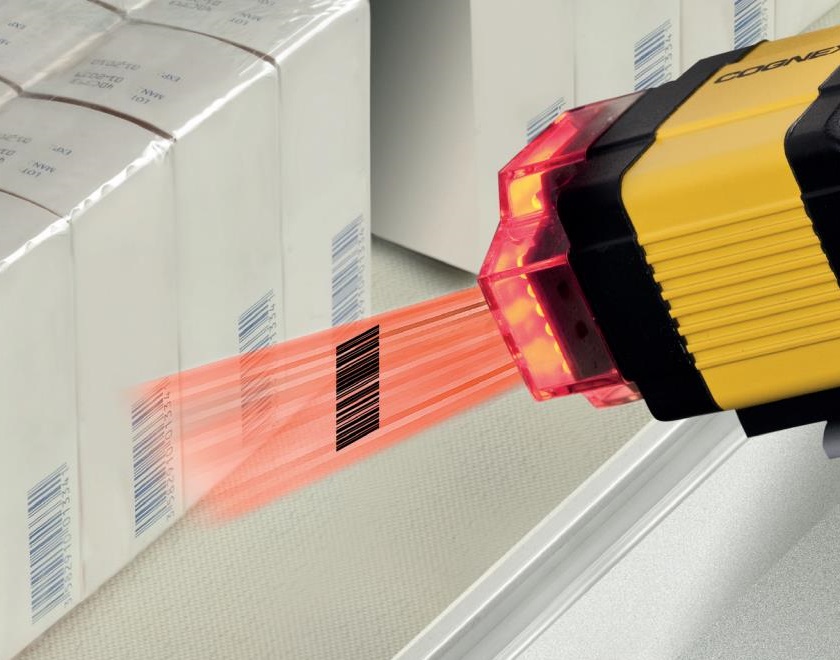
Les normes
Les codes à barres linéaires sont définis dans la norme internationale ISO/IEC 15420 et le code DataMatrix bidimensionnel dans la norme ISO/IEC 16022.
Lors du contrôle de la qualité d'impression, appelé vérification, les normes ISO/IEC 15415 et 15416 sont déterminantes. Si les codes ne sont pas imprimés mais apposés d'une autre manière, d'autres normes telles que AIM DPM ou AS9132 peuvent également être appliquées.
Le contenu ou la structure des données est défini dans les GS1 General Specifications (GS1 est l'organisation qui a succédé à EAN). La norme ANS_MH10.8.2 détermine comment un code doit être structuré du point de vue du contenu. Les différents champs sont identifiés par des "Application Identifiers" (AI) et le contenu de ces champs doit également être conforme. Les AI courants sont par exemple le GTIN (Global Trade Item Number, qui permet d'identifier les produits de manière univoque dans le monde entier), le numéro de lot, la date d'expiration, etc.
Vérification et validation du code
La vérification consiste à évaluer la qualité du code appliqué. Il s'agit de s'assurer que les codes peuvent être relus en toute sécurité à tout moment par des lecteurs de différents fabricants. Les normes ISO/CEI 15415 et 15426 définissent la manière de mesurer la qualité et conviennent bien aux impressions sur les boîtes pliantes. En revanche, ces normes ne sont pas adaptées au marquage direct de pièces métalliques. Dans l'industrie automobile, par exemple, on préfère la norme AIM DPM.
Pour vérifier la conformité du contenu du code avec le standard GS1, le code est validé. Le code est lu, les différents AI et les champs correspondants sont identifiés et leur exactitude est ensuite vérifiée. Certains pays ont déjà adopté depuis longtemps des directives supplémentaires qui exigent un contrôle spécifique au pays.
Le "DataMatrix Code Verifier" permet aussi bien la vérification selon la norme ISO/IEC 15415 que la validation GS1 pour des morceaux de carton ou des boîtes pliantes entières. La norme exige que le code soit contrôlé et évalué dans cinq positions de rotation déterminées lors de la vérification, ce qui est très simple à l'aide de l'appareil développé et breveté par Compar.
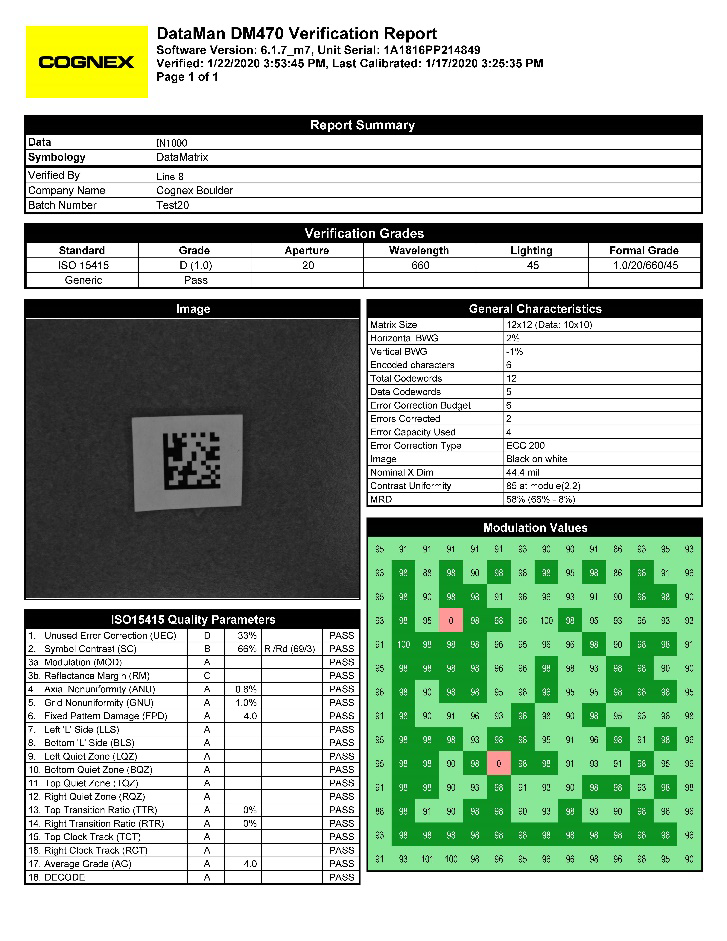
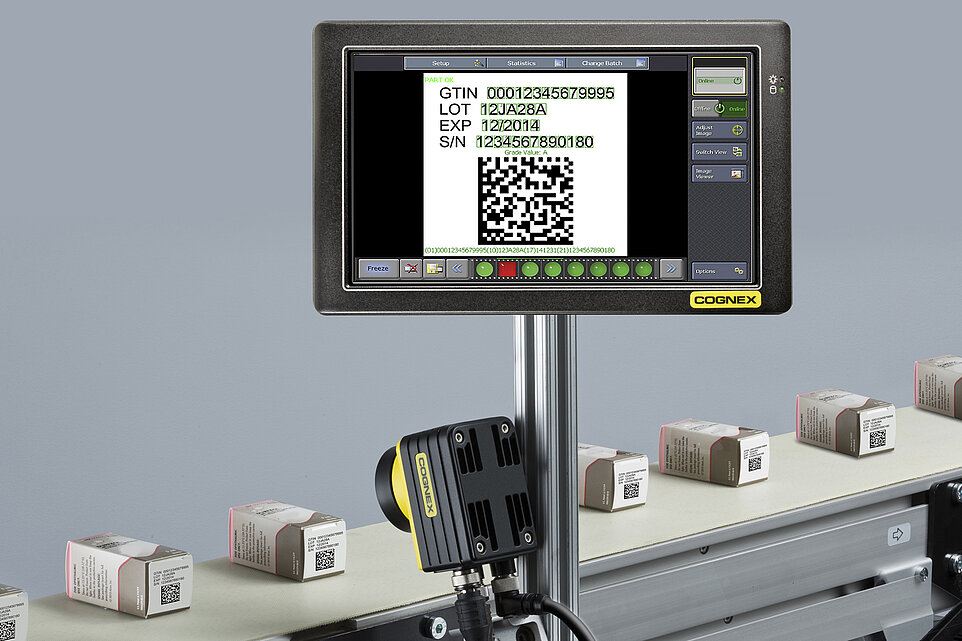
Grading en ligne et OCV
Pour le contrôle sur la ligne de production, il faut des systèmes rapides qui combinent différentes fonctionnalités. Un exemple est la vérification d'un code DataMatrix suivie de la vérification du contenu imprimé en caractères explicites à côté. Contrairement à la vérification selon la norme ISO/IEC 15415, le code n'est enregistré, lu et évalué que dans une seule position de rotation. Pour la vérification des caractères, les valeurs du code DataMatrix sont reprises et les caractères sont vérifiés dans les champs correspondants quant à l'exactitude de l'information et à la qualité d'impression. Comme le texte à vérifier est déjà connu après la lecture du code, on parle ici d'Optical Character Verification ou OCV.
Le grading en ligne a pour but de garantir une qualité constante dans la production. Il requiert la conformité aux normes.
La traçabilité
De nos jours, pour des produits comme les médicaments, il est possible de marquer individuellement chaque boîte et d'archiver les données de production et de contrôle correspondant au numéro de série. Si le codage est correct en termes de contenu et de qualité, une boîte peut être retirée des rayons et identifiée par exemple à l'aide d'un lecteur manuel. Il est alors possible de retracer comment, quand et dans quelles conditions le produit a été fabriqué et contrôlé et par quels canaux il a été vendu.
Le fournisseur des systèmes de contrôle est en mesure d'enregistrer ses exigences de contrôle et les résultats des contrôles de qualité en production de manière infalsifiable. Si les produits sont identifiés ultérieurement, le fabricant est ainsi en mesure de fournir les preuves nécessaires en cas de responsabilité du fait des produits. En outre, la traçabilité des canaux de vente facilitera la tâche des contrefacteurs et autres malfaiteurs.
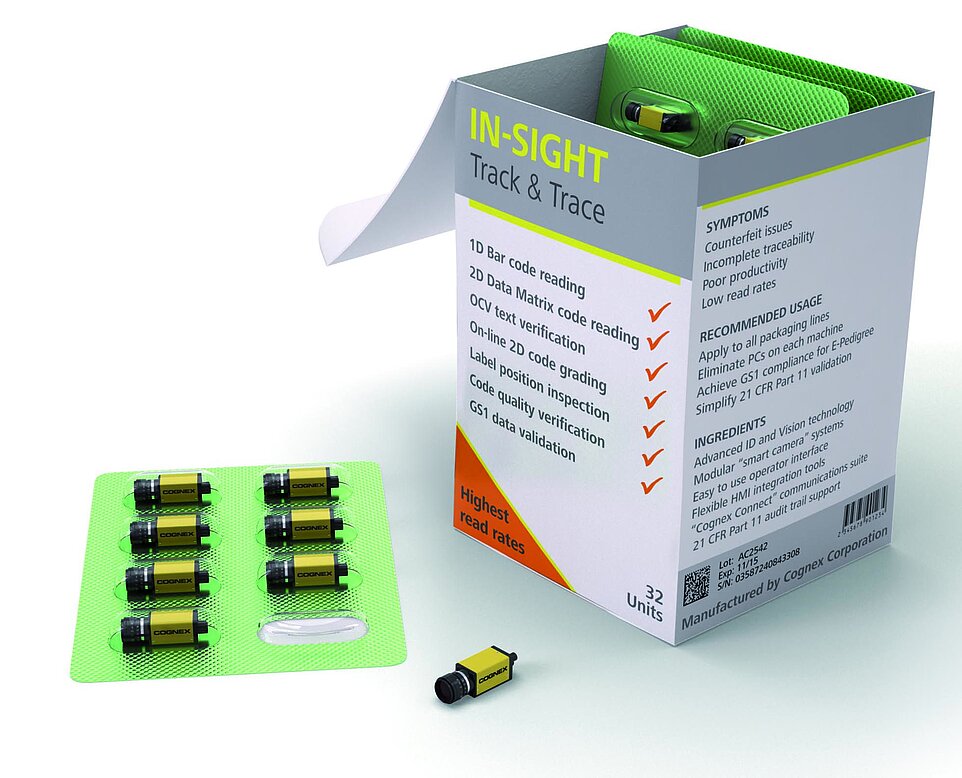
Les différentes possibilités décrites ci-dessus ne sont pas des utopies mais sont actuellement mises en œuvre aujourd'hui. Compar est le premier intégrateur de systèmes Cognex en Europe et fournit des solutions innovantes dans le domaine de la vision industrielle et de l'identification.